How Does CNC Machining Differ from Traditional Machining?
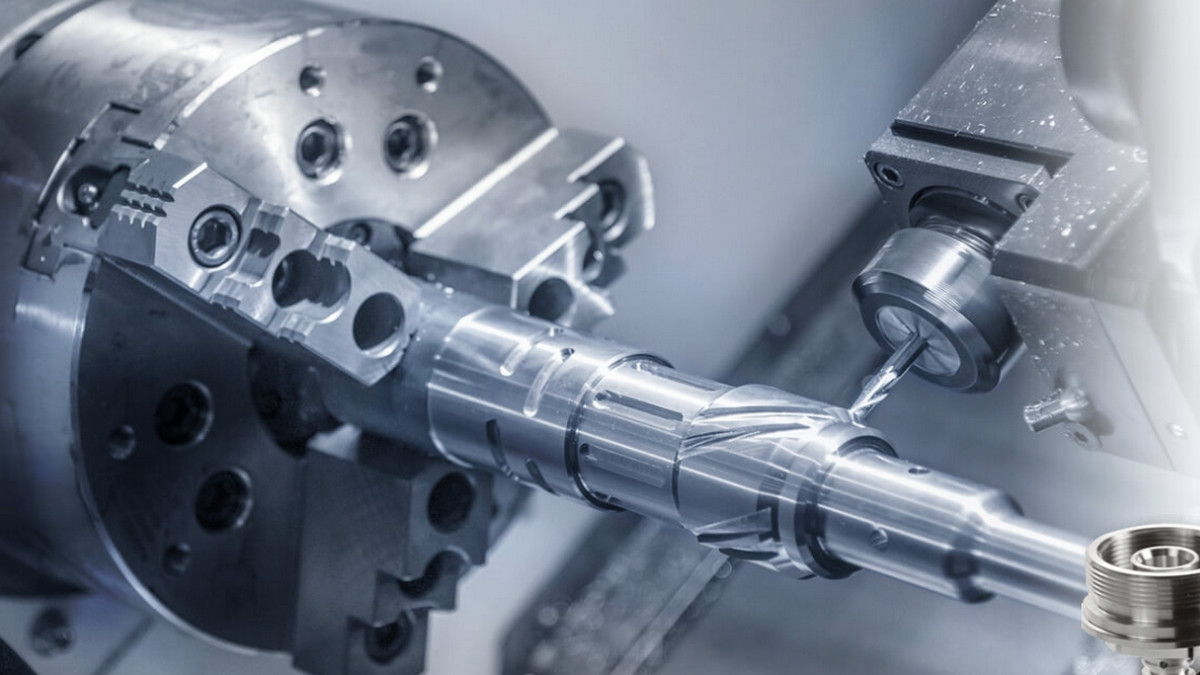
When comparing precision CNC machining services with traditional machining methods, it's essential to understand their distinct differences and advantages. As industries advance, machining techniques have evolved to offer more efficient, accurate, and scalable solutions. CNC machining (Computer Numerical Control) has revolutionized the manufacturing process by automating tasks that were once manually executed. This automation ensures higher precision, speed, and reliability compared to traditional methods. At Newtop Industry Group, we provide top-notch precision CNC machining services tailored to meet diverse industry needs.
The Basics of Traditional Machining
Traditional machining refers to a manual or semi-automatic method where an operator uses various tools like lathes, mills, drills, and grinders to shape materials. It relies heavily on the skill and experience of the machinist. The process involves manually adjusting the cutting tools and controlling the machine to shape a material into the desired form.
Some common characteristics of traditional machining include:
• Manual Control: Machinists control the cutting tools and machines manually.
• Limited Accuracy: Since it depends on human skill, the accuracy is limited to how well the machinist can handle the tool.
• Time-Consuming: Manual adjustments mean more time is spent on setup and operation.
• Less Reproducibility: Each part may slightly differ from the others due to human error.
Though traditional machining methods are still in use, they are less efficient when it comes to handling complex, precise, or high-volume projects.
CNC Machining: A Technological Leap Forward
CNC machining represents a technological breakthrough in the manufacturing industry. Using computer programs to control machining tools, CNC machines can create complex parts with remarkable precision and speed. The process begins by designing the part using CAD (Computer-Aided Design) software, followed by generating a CAM (Computer-Aided Manufacturing) file, which instructs the CNC machine on how to shape the material.
Key aspects of CNC machining include:
• Computer Automation: The entire machining process is controlled by computers, reducing the need for manual labor.
• High Precision: CNC machines follow exact instructions, leading to precise cuts and shapes.
• Consistency: Unlike traditional methods, CNC machining can produce identical parts over and over with little to no variation.
• Speed: Automated machines work faster than manual setups, making the production process quicker and more efficient.
At Newtop Industry Group, we specialize in precision CNC machining services, ensuring that every part we manufacture adheres to the highest standards of accuracy.
Key Differences Between CNC and Traditional Machining
1. Automation vs. Manual Control
The most significant difference between CNC and traditional machining is the level of automation. In traditional machining, machinists must manually control the tools and machines, which is time-consuming and prone to human error. On the other hand, CNC machining is fully automated, meaning computers control the machines based on programmed designs. This leads to greater efficiency and precision.
2. Precision and Accuracy
In traditional machining, the accuracy of the finished product depends on the machinist's expertise. Even the most skilled machinists can't match the level of precision offered by CNC machines. Precision CNC machining services use advanced software to ensure that the design specifications are followed exactly, with tolerances as tight as a few microns. This is crucial for industries like aerospace, automotive, and medical, where even the smallest discrepancies can lead to failure.
3. Reproducibility
Reproducing identical parts using traditional machining methods can be challenging due to the manual adjustments required for each piece. CNC machining, however, excels in repeatability. Once a design is programmed into the machine, it can produce hundreds or thousands of identical parts without variation, a feature that's particularly beneficial for mass production.
4. Complexity
Traditional machining methods struggle with complex geometries and intricate designs. The process often requires several different tools and multiple setups, which increases the chance of error. Precision CNC machining services, by contrast, can handle complex shapes and intricate features with ease. The CAD/CAM software allows for the creation of parts with complex 3D geometries that would be impossible or impractical with traditional methods.
5. Speed and Efficiency
Traditional machining takes longer because it requires constant human intervention for tool changes, part adjustments, and measurements. CNC machines, once programmed, can work continuously without interruption, greatly increasing the speed of production. This not only improves efficiency but also reduces costs associated with labor and downtime.
6. Customization and Flexibility
While traditional machining can be flexible in small-batch or custom projects, it lacks the scalability of CNC machining. With precision CNC machining services, you can quickly change designs or adjust specifications within the software without the need to manually retool the machine. This flexibility is crucial for industries that need to adapt to rapidly changing market demands or that require customized solutions.
Benefits of CNC Machining Over Traditional Methods
1. Higher Productivity: The speed and automation of CNC machines increase production rates, making it easier to meet tight deadlines.
2. Lower Costs: Although the initial investment in CNC machinery is higher, the reduced labor costs and increased efficiency make it more cost-effective in the long run.
3. Enhanced Safety: Since CNC machines are automated, the operator doesn’t need to be as involved in the process, reducing the chances of accidents or injuries in the workplace.
4. Precision and Quality: CNC machines offer unmatched precision, making them ideal for industries that demand high levels of accuracy, such as medical devices or aerospace components.
5. Minimal Waste: CNC machines are highly efficient and only use the necessary amount of material, reducing waste and contributing to a more sustainable manufacturing process.
Why Choose Newtop Industry Group for Precision CNC Machining Services?
At Newtop Industry Group, we are committed to delivering high-quality precision CNC machining services tailored to your specific requirements. With years of experience in the industry, we understand the importance of precision, speed, and reliability. Our state-of-the-art CNC machines, combined with our skilled team of engineers, ensure that every project we undertake is completed to the highest standards.
Whether you need a single prototype or a large production run, we have the capabilities to meet your needs. Our precision CNC machining services offer:
• Advanced technology: We use the latest CAD/CAM software and CNC machines to ensure precise and efficient production.
• Custom solutions: We work closely with our clients to understand their unique needs and offer custom machining solutions.
• Quality control: Every part we produce undergoes rigorous quality checks to ensure it meets the required specifications.
Conclusion
CNC machining offers a range of benefits over traditional machining methods, from increased precision and efficiency to the ability to produce complex parts at scale. At Newtop Industry Group, our precision CNC machining services are designed to meet the diverse needs of industries that require high-quality, accurate, and reliable machining solutions. Whether you're in the aerospace, automotive, or medical industry, CNC machining is the key to unlocking faster production times and superior product quality.