What Materials Are Used in Heavy Metal Fabrication?
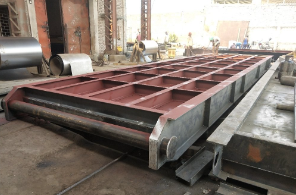
When it comes to heavy metal fabrication, the choice of materials plays a crucial role in determining the durability, functionality, and overall quality of the end product. At Newtop Industry Group, we understand that the key to successful fabrication lies in selecting the right materials based on the project’s specific needs. This article explores the various types of materials commonly used in heavy metal fabrication, and their advantages in the fabrication process.
1. Steel: The Backbone of Heavy Metal Fabrication
Steel is the most common material used in heavy metal fabrication due to its strength, versatility, and affordability. There are various types of steel that are employed depending on the application:
• Carbon Steel: This type of steel is composed mainly of iron and carbon, and it’s known for its toughness and ability to withstand wear and tear. Carbon steel is ideal for creating structural components such as beams, frames, and pipes.
• Stainless Steel: With the addition of chromium, stainless steel is highly resistant to rust and corrosion, making it suitable for environments where exposure to moisture and chemicals is a concern. It is widely used in industries like food processing, pharmaceutical manufacturing, and chemical plants.
• Alloy Steel: This type of steel contains other elements such as nickel, chromium, and manganese to enhance specific properties like hardness, toughness, and wear resistance. Alloy steel is used in applications where additional strength and durability are required, such as in heavy machinery and construction equipment.
The flexibility and durability of steel make it a cornerstone of heavy metal fabrication. At Newtop Industry Group, we specialize in fabricating steel components that meet the highest industry standards.
2. Aluminum: Lightweight but Strong
Aluminum is another widely used material in heavy metal fabrication due to its lightweight properties combined with high strength. While it may not be as strong as steel, aluminum’s excellent resistance to corrosion makes it a preferred choice in industries like aerospace, automotive, and marine.
Some key benefits of aluminum include:
• Corrosion Resistance: Aluminum naturally forms a protective oxide layer, which makes it highly resistant to rust, even in harsh environments like salty or humid conditions.
• Lightweight: Aluminum’s low density means that it can be used in applications where weight reduction is a priority, such as in aircraft, automobiles, and marine vessels.
• Workability: Aluminum is easy to machine, cut, and weld, which makes it an ideal material for complex designs and intricate shapes.
Newtop Industry Group has extensive experience in fabricating high-quality aluminum components that offer strength without the added weight.
3. Copper: A Material for Precision and Electrical Conductivity
Copper, known for its excellent electrical conductivity and resistance to corrosion, is often used in heavy metal fabrication for projects that require precision and durability. While copper is not as strong as steel or aluminum, its ability to conduct electricity makes it indispensable in electrical wiring, transformers, and power generation equipment.
Key characteristics of copper include:
• High Electrical Conductivity: Copper is the go-to material for electrical applications, providing efficient conductivity for power transmission.
• Thermal Conductivity: Copper’s ability to conduct heat efficiently makes it useful in heat exchangers, cooling systems, and other applications where heat dissipation is critical.
• Corrosion Resistance: Copper is naturally resistant to corrosion, especially in moist environments, making it a long-lasting choice for plumbing, roofing, and industrial components.
At Newtop Industry Group, we leverage the unique properties of copper to create high-precision, long-lasting components.
4. Titanium: Superior Strength and Resistance
Titanium is a material known for its incredible strength-to-weight ratio, making it a popular choice in heavy metal fabrication for industries that require both lightness and strength, such as aerospace, medical, and military applications. Despite being relatively lightweight, titanium boasts a level of strength comparable to that of steel.
Some of the advantages of titanium include:
• Corrosion Resistance: Titanium is highly resistant to corrosion, even in harsh environments such as seawater, making it ideal for marine and chemical applications.
• High Strength: Titanium has a remarkable ability to withstand extreme forces and stress, making it suitable for critical structural applications.
• Biocompatibility: Titanium’s non-reactive nature makes it a material of choice in medical implants and prosthetics, as it does not react with the human body.
At Newtop Industry Group, we offer titanium fabrication services to meet the demanding needs of advanced industries.
5. Nickel Alloys: The Ultimate for Heat and Corrosion Resistance
Nickel alloys are frequently used in heavy metal fabrication due to their exceptional resistance to heat, corrosion, and oxidation. These alloys are often chosen for high-temperature environments and industries that handle corrosive substances, such as power plants, oil refineries, and chemical processing facilities.
Some important nickel alloys include:
• Inconel: Known for its ability to withstand extreme temperatures and corrosive environments, Inconel is commonly used in jet engines, gas turbines, and other high-heat applications.
• Monel: This nickel-copper alloy is highly resistant to corrosion, making it an excellent choice for marine applications and chemical plants.
• Hastelloy: With enhanced corrosion resistance, especially in acidic environments, Hastelloy is often used in chemical processing and pharmaceutical industries.
Newtop Industry Group utilizes nickel alloys for fabricating components that must endure the toughest conditions.
6. Brass and Bronze: Durable and Decorative
Brass and bronze are copper-based alloys commonly used in heavy metal fabrication for their unique blend of durability and aesthetic appeal. These materials are particularly popular for decorative elements, as well as functional components in industries like plumbing, electrical, and marine.
• Brass: A copper-zinc alloy, brass is known for its bright, gold-like appearance and excellent machinability. It’s often used for fittings, valves, and decorative applications.
• Bronze: A copper-tin alloy, bronze is renowned for its strength and wears resistance, making it ideal for bearings, bushings, and marine hardware.
At Newtop Industry Group, we craft high-quality brass and bronze components that offer both functionality and elegance.
Conclusion
Choosing the right materials is a critical step in the heavy metal fabrication process. The wide variety of metals available, from steel and aluminum to copper and nickel alloys, offers diverse solutions to meet the needs of various industries. At Newtop Industry Group, we have the expertise to select and fabricate the ideal material for your project, ensuring strength, durability, and cost-effectiveness. Whether you need lightweight aluminum parts for aerospace or corrosion-resistant nickel alloys for chemical processing, we are equipped to deliver superior results tailored to your specific requirements.
Reach out to Newtop Industry Group today for all your heavy metal fabrication needs. Our team of professionals is ready to help you choose the perfect materials for your project, ensuring the highest levels of quality and performance.