What are the Benefits of Using Aluminum in CNC Machining?
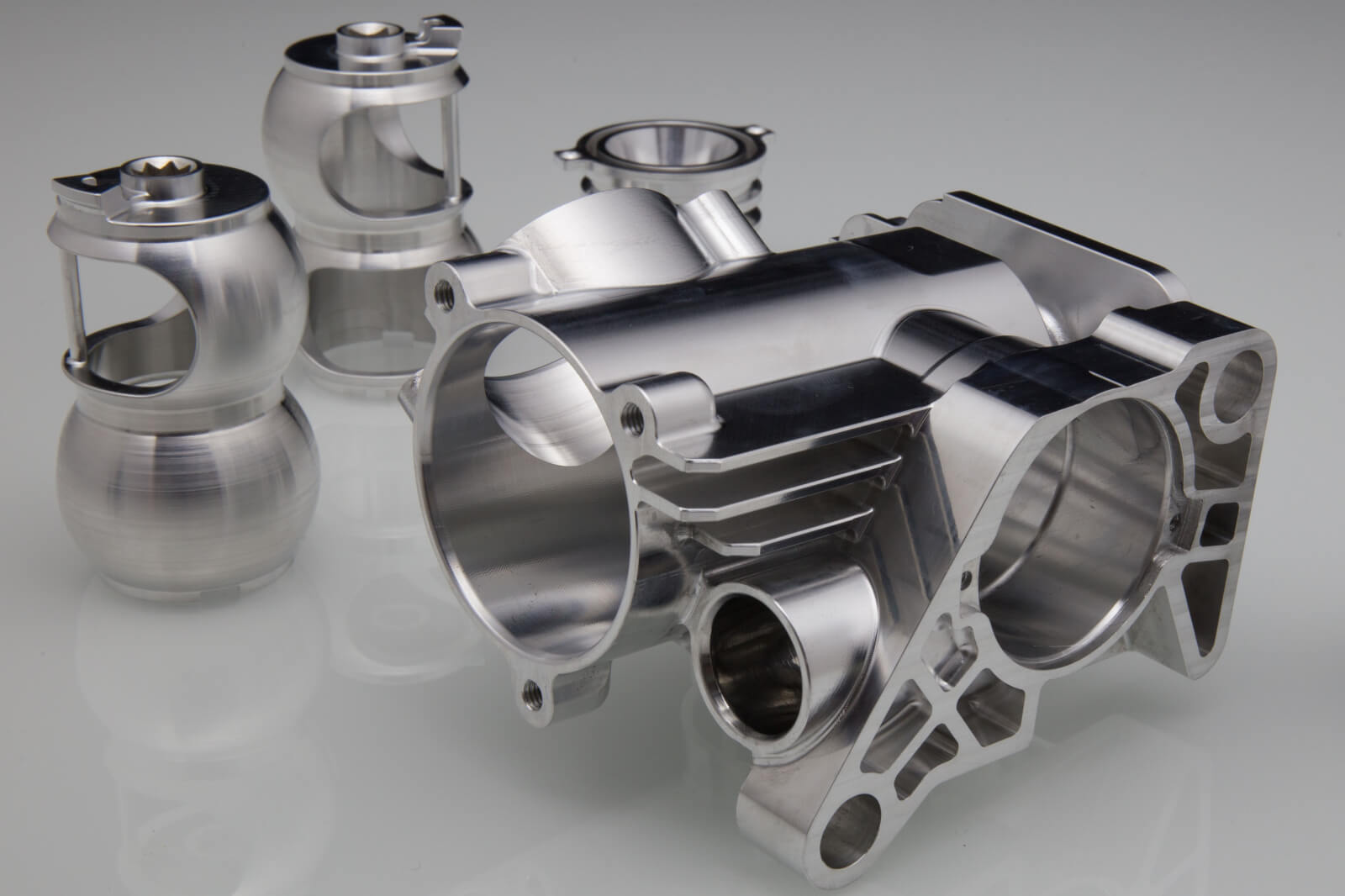
Aluminum has become one of the most popular materials used in CNC machining due to its unique properties and versatility. At Newtop Industry Group, we specialize in manufacturing aluminum CNC machining parts, offering high precision, durability, and efficiency. In this article, we’ll explore the various benefits of using aluminum in CNC machining and why it is the preferred choice for many industries, including aerospace, automotive, and electronics.
1. Lightweight and Strong
One of the key benefits of aluminum is its lightweight nature, making it an excellent choice for industries where weight reduction is crucial, such as aerospace and automotive. Despite its lightness, aluminum offers impressive strength, making it a reliable material for creating robust aluminum CNC machining parts. The combination of these characteristics ensures that products made from aluminum are durable yet easy to handle.
This lightweight strength ratio allows manufacturers to produce parts that meet rigorous structural requirements without adding excess weight, which can improve performance and efficiency, especially in vehicles and aircraft.
2. High Corrosion Resistance
Aluminum naturally forms a protective oxide layer on its surface, providing a high degree of corrosion resistance. This makes aluminum an ideal material for CNC machining, especially for parts exposed to harsh environments or conditions that could lead to rust or deterioration. Products made from aluminum CNC machining parts can withstand moisture, chemicals, and other elements, making them suitable for marine, automotive, and outdoor applications.
In industries where durability and longevity are essential, the corrosion resistance of aluminum plays a pivotal role in maintaining the functionality and appearance of the parts over time.
3. Excellent Machinability
Aluminum’s machinability is one of its standout features. It can be easily cut, shaped, and drilled with CNC machines, making it ideal for producing high-precision components. This not only speeds up the production process but also ensures consistency and accuracy in every batch of aluminum CNC machining parts. Aluminum’s softness compared to other metals, like steel, reduces tool wear, further improving cost efficiency in machining operations.
Manufacturers often prefer aluminum for projects requiring intricate details and tight tolerances. Its machinability reduces production times and allows for quicker delivery of complex parts without sacrificing quality.
4. Cost-Effective Material
Compared to other metals used in CNC machining, such as titanium or stainless steel, aluminum is more affordable. Its wide availability and relatively low production cost make it an economical choice for both small-scale and mass production projects. The cost-effectiveness of aluminum CNC machining parts makes it a go-to material for companies looking to balance high performance with budget considerations.
In addition to the raw material costs, the shorter machining times and reduced tool wear associated with aluminum contribute to lower overall manufacturing expenses, making it a cost-efficient solution for businesses across multiple industries.
5. Excellent Thermal and Electrical Conductivity
Aluminum is an excellent conductor of both heat and electricity. This makes it a suitable material for industries such as electronics and electrical engineering, where efficient heat dissipation is critical. Aluminum CNC machining parts can be used in heat sinks, electronic enclosures, and other components requiring high thermal conductivity.
Its ability to rapidly dissipate heat also benefits applications in automotive and aerospace industries, where managing heat buildup is crucial for safety and performance. Additionally, aluminum’s electrical conductivity makes it ideal for wiring, connectors, and other parts in electrical systems.
6. Recyclability and Sustainability
Aluminum is a fully recyclable material, meaning that it can be melted down and reused without losing its quality. This contributes to sustainable manufacturing practices and reduces waste, which is increasingly important in today’s eco-conscious world. Using aluminum CNC machining parts supports environmental initiatives and helps companies reduce their carbon footprint.
At Newtop Industry Group, we are committed to sustainable production processes, and working with aluminum allows us to provide our clients with eco-friendly solutions while maintaining the highest standards of quality and performance.
7. Versatility in Applications
Aluminum’s combination of properties – lightweight, strength, corrosion resistance, and machinability – makes it highly versatile across a wide range of applications. Whether you need aluminum CNC machining parts for aerospace components, automotive parts, electronics, or medical devices, aluminum can meet the requirements of various industries.
Its adaptability allows for the creation of parts that need to withstand extreme conditions, such as high temperatures, mechanical stress, or chemical exposure. This versatility is why aluminum remains a top choice in the manufacturing sector.
8. Customization and Design Flexibility
Another benefit of using aluminum in CNC machining is the high degree of customization it offers. Aluminum can be easily anodized or treated for different finishes, adding aesthetic appeal and additional protective layers. This is particularly useful in industries where both function and appearance matter.
With aluminum CNC machining parts, manufacturers can produce parts in a variety of shapes, sizes, and surface finishes, meeting the specific needs of each project. At Newtop Industry Group, we offer custom CNC machining services that can accommodate even the most complex designs while ensuring precision and quality in every part.
9. Shorter Lead Times
Aluminum’s excellent machinability, combined with its availability and cost-effectiveness, leads to shorter lead times for CNC machining projects. At Newtop Industry Group, we understand that time is critical in manufacturing, which is why we prioritize quick turnaround times for our clients.
By choosing aluminum CNC machining parts, businesses can reduce the time it takes to go from concept to final product, helping them stay ahead in competitive markets. The efficiency of aluminum machining translates to faster production cycles and timely delivery of high-quality parts.
Conclusion
The benefits of using aluminum in CNC machining are clear. From its lightweight and strong nature to its excellent corrosion resistance and cost-effectiveness, aluminum is a material that meets the demands of modern industries. At Newtop Industry Group, we specialize in providing high-quality aluminum CNC machining parts, offering precision, reliability, and customization to meet the unique needs of each client.