12 Reasons You Shouldn’t Invest in Aluminum Machining
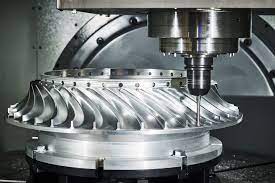
At Newtop Industry Group, we specialize in precision manufacturing, including aluminum machining. While aluminum is a widely used material in industries like aerospace, automotive, and electronics, investing in its machining process comes with several challenges. Before diving into the world of aluminum machining, here are 12 key reasons why it might not be the best investment for you.
1. High Initial Investment Costs
Setting up an aluminum machining facility requires substantial upfront investment in CNC machines, tooling, and raw materials. The cost can be a significant barrier for businesses looking for cost-effective solutions.
2. Rapid Tool Wear
Aluminum’s properties, such as its softness and high thermal conductivity, cause tools to wear out quickly. This leads to frequent replacements and increased operational costs.
3. Chip Management Challenges
Unlike other metals, aluminum produces long, stringy chips that can clog machinery. Efficient chip evacuation systems are needed, adding to the complexity and cost of machining.
4. Thermal Expansion Issues
Aluminum expands significantly with temperature fluctuations, making precision machining difficult. Specialized techniques and cooling systems are required to maintain accuracy.
5. Surface Finish Difficulties
Although aluminum is known for its smooth finish, achieving a flawless surface requires extra effort, including precise tool geometry and specialized coatings, increasing production costs.
6. High Scrap Rates
Due to its lightweight nature and tendency to deform under pressure, machining aluminum often results in high scrap rates, leading to material wastage and loss of profit.
7. Complex Post-Processing Requirements
Machined aluminum parts often require additional finishing processes such as anodizing or powder coating to enhance durability, adding to time and cost.
8. Risk of Contamination
Aluminum is susceptible to contamination from other metals, which can affect its performance. Strict handling procedures must be in place to prevent this issue.
9. Limited Structural Strength
Compared to steel or titanium, aluminum has lower strength and wear resistance. This makes it unsuitable for heavy-load applications, limiting its use in some industries.
10. Specialized Workforce Required
Successful aluminum machining requires experienced operators who understand material properties, cutting strategies, and surface treatment. Hiring and training skilled workers add to operational expenses.
11. Environmental Concerns
The process of machining aluminum generates waste material and energy consumption, raising concerns about sustainability and regulatory compliance.
12. Market Competition
Due to its widespread use, the aluminum machining industry is highly competitive, making it difficult for newcomers to establish themselves and achieve profitability.
Conclusion
While aluminum is a versatile and essential material, its machining presents various challenges that may not make it the best investment choice for every business. At Newtop Industry Group, we provide expert guidance and solutions to navigate these challenges effectively. If you're considering aluminum machining, let our team help you make an informed decision.